Explosion Isolation, Mechanical
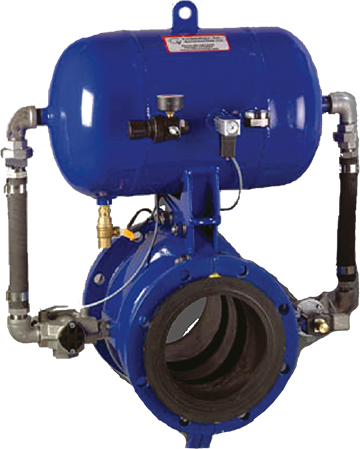
Selection of the right mechanical isolation valve depends upon the maximum pressure that it must resist in the event of a deflagration. The following general rules should be followed:
Process Equipment Protection Basis | Mechanical Isolation Guidelines |
Containment | The mechanical isolation device applied must be designed to survive the maximum explosion pressure for the process material, Pmax. In addition, all of the piping and equipment upstream of the isolation device must also be designed to accept Pmax. This may require a design pressure as high as 230psig / 16 Bar. |
Venting | The mechanical isolation device applied must be designed to survive the reduced explosion pressure of a vented deflagration, Pred. In addition, all of the piping and equipment upstream of the isolation device must also be designed to accept Pred. This will typically require a design pressure as low as 3 psig / 0.2 Bar. |
Suppression | The mechanical isolation device applied must be designed to survive the reduced explosion pressure of a suppressed deflagration, Pred. In addition, all of the piping and equipment upstream of the isolation device must also be designed to accept Pred. This will typically require a design pressure as low as 2 or 3 psig / 0.14~0.2 Bar. |
There are significant differences regarding the installation requirements for mechanical isolation devices designed for low or high pressure shut off. The weight of the protection equipment is much higher for a device that will accept Pmax. For typical isolation valve sizes, a weight comparison is provided below:
Normal Size | Low Pressure Isolation Valve | High Pressure Isolation Valve | |||
Inch | mm | Pounds | Kg | Pounds | Kg |
4 | 100 | 57 | 26 | 150 | 69 |
6 | 150 | 96 | 44 | 195 | 89 |
8 | 200 | 151 | 69 | 305 | 140 |
10 | 250 | 297 | 136 | 415 | 190 |
In addition to the weight of the device, the recoil forces must be managed by the ducting and its support system.
Designed to respond in the manner of an ‘air bag’ in a vehicle, when the IVE isolation valve is directed to close, an inflatable bladder immediately fills the body cavity to stop product flow and arrest flame propagation. This operating mode minimizes the reaction forces generated by the IVE valve. The BS&B Type IVE valve is available in sizes from 4” to 16” nominal diameter (100mm to 400mm). Activation of the valve can be by BS&B supplied pressure or optical sensors.